The Manufacturing Process of Vinyl Commercial Wall Panels: Here’s Everything You Need to Know :
- duramaxpvcpanels
- Feb 15, 2024
- 3 min read
Vinyl commercial wall panels are made by mixing and processing PVC, expanded as polyvinyl chloride resin along with other additives. Here, we will be taking a look at the step-by-step production process of vinyl panels. So, let’s start.
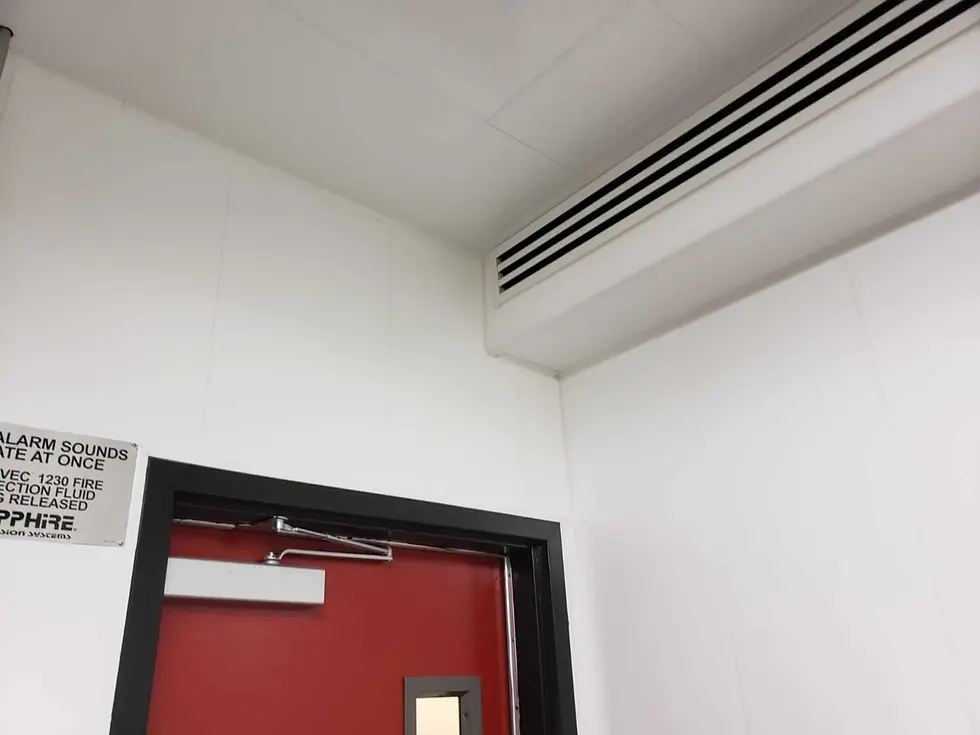
The Procedure
Preparing the Raw Material
You first need to prepare the PVC resin, which will act as the primary raw material in the manufacture of vinyl panels. Also, there are several manufacturers in the US that mix other chemical additives, like pigments, fillers, plasticizers, and stabilizers, to boost the performance of vinyl wall panels.
Material Mixing
The vinyl resin and other additives are then sent to an extruder or mixer for blending. During this step, the additives are uniformly dispersed in the vinyl resin, thereby ensuring the plastic panel's stability and consistency.
Extrusion Molding
Then, the mixed vinyl resin is pressed out into wall panels of different shapes and sizes with the help of an extruder. This is a constant process, and the wall panels are produced from the exit of the extruder, just like pressed-out long strips.
Cooling and Solidification
The extruded vinyl commercial wall panels undergo a cooling process that allows them to stabilize and solidify. This is performed on a conveyor belt, where the PVC panel is conveyed until completely cured.
Cutting and Shaping
The pressed-out long strips of vinyl panels are then cut to the required length, shaped, and pruned to obtain the final product.
Surface Treatment
Some vinyl panels may need surface treatments, like embossing, stickers, printing, etc., to create different patterns and textures.
Packaging and Shipping
Finally, the finished vinyl wall panels are packed by PVC wall panel suppliers in the US, after which they are shipped to the end customers.
We would like to point out here that different manufacturers may adopt different formulations and processes to cater to the needs and preferences of different customers and markets. So, the exact manufacturing process may vary slightly. Overall, PVC panel manufacturing is a relatively simple task, thereby making the material the most sought-after and affordable wall covering material. Now that you have a fairly good idea of the manufacturing process of PVC panels let’s take a look at some of the benefits you can reap from installing these panels in your commercial space.
The Good Ones
Lightweight and Easy to Transport
PVC panel is one of the lightest paneling materials used in ceilings and walls.
These panels are extremely sturdy, lightweight, and durable.
They are easy to transport, handle, and install without creating a dusty environment during installation.
Extremely Durable
Vinyl wall panels are sturdy, robust, and highly durable. These panels can last for over ten decades without bending or warping.
Brilliant Moisture Resistance
PVC commercial wall panels are made up of waterproof materials, which makes them highly moisture-resistant.
These panels are a good fit for covering the ceilings and walls of wet spaces like car wash garages, basements, and bathrooms, which are highly susceptible to moisture.
Also, the fact that these panels have an interlocking tongue-and-groove mechanism prevents water ingress to a great extent.
Since these panels are water-resistant, they prevent the growth and proliferation of mold, mildew, and bacteria on the panel surfaces.
Final Take:
If you are looking for high-grade vinyl panels in the US, all you need to do is perform a quick search online and look for PVC wall panel suppliers in the US offering moisture-resistant PVC panels at highly affordable prices. Get in touch with them, and you will be good to go.
Comentários